Power Tools
Power Tool Parts Manufacturer
We manufacture power tool components for consumer products including chain saws, drills, impact drivers, lawn mowers, and more. With support from prototype to production, we can help with all your projects. For custom manufacturing, request a quote. For stock springs, fasteners, and more, visit our online store.
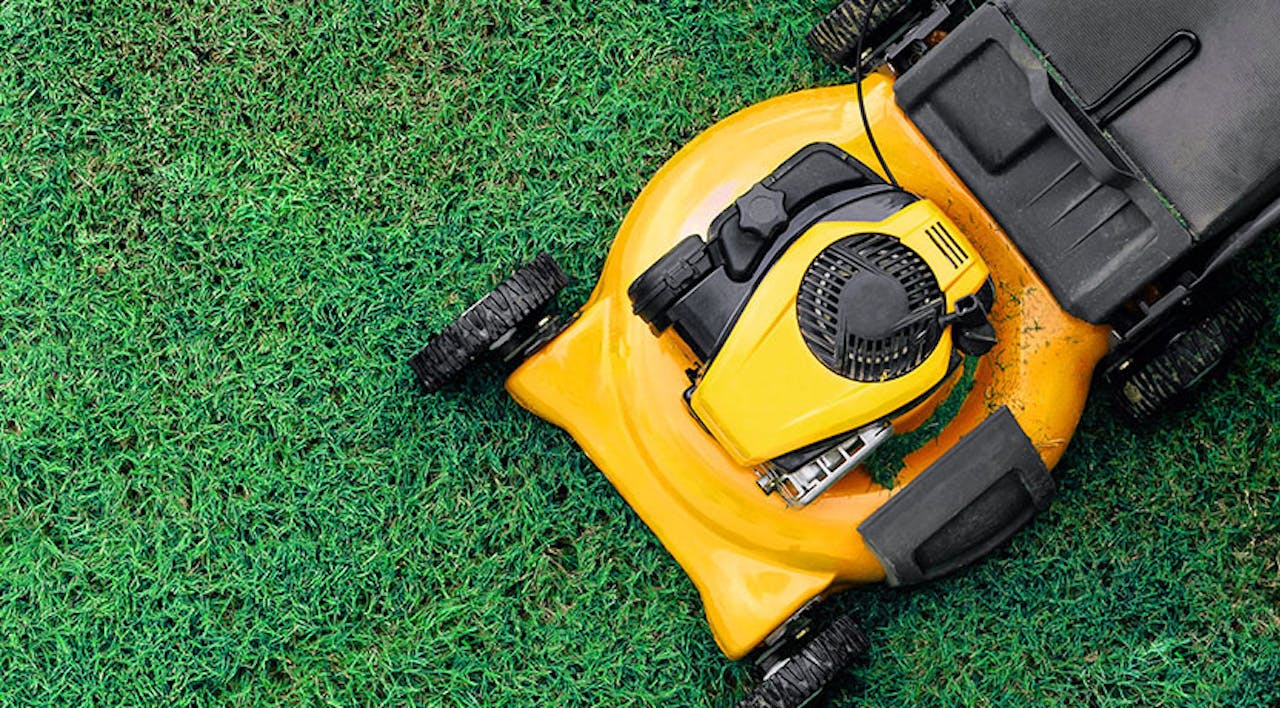
Power Tool Components
Power equipment often operates in demanding conditions, including extended use and extreme environments. At MW Components, we design, engineer, and test our lightweight components to provide durability and consistent operation over a long life.
The Most Efficient Manufacturing with the Latest Technology
With over 30 locations, our manufacturing facilities offer the latest technology, including Swiss turning with diameters from 0.188” to 1.250”, CNC milling, honing, grinding, and more. Our team has over 50 years of experience manufacturing precision products such as hot and cold wound springs, fourslide metal stampings, and Belleville washers. These quality products have given us a reputation as a top US-based power tool manufacturer and led us to support some of the largest consumer tool brands in the world.
Power Tools at a Glance
YEARS SERVING INDUSTRY
50+
Custom and Ready-to-Ship, Stock Power Tool Components
MW Components designs and manufactures highly engineered springs and metal component systems for the world’s leading brands of power tools and consumer products. We collaborate with and support our customers’ development and engineering efforts. Get in touch with us for custom manufacturing of power tool components for chainsaws, leaf blowers, handheld and tabletop drills, lawn mower, circular and table saws, routers, impact drivers, and more.
MW’s power tool components are also available as stock and standard products, many of which are used in operator controls and engine management for maintenance, lawn, and garden care applications. Our customers rely on us for a range of products, including critical safety applications, control purposes such as power triggers, on/off switches, throttle controls, drive-line controls, and speed control.
What We Offer
Reliable Manufacturing Services
Our precision components are produced and delivered from multiple MW Components locations across the United States. While each of our manufacturing facilities offers different capabilities and specialties, they all work together using the latest equipment and technology.
Quality Materials
From music wire, copper, and alloys to specialty materials like Elgiloy® and A286, our team has experience working with a variety of high-quality metals.
A Manufacturing Partner You Can Rely On
We take pride in delivering high-quality value on time and at the right price. We will work closely with you to develop components to match your exact requirements, reduce your costs, and support your logistics efforts. Our power tool components include brackets, hammer cams, timing shaft springs, throttle rods and springs, pneumatic manifolds, reverse valves, and more. We'll work with you to create the highest quality components for power tools, lawn care and garden maintenance, and other applications.
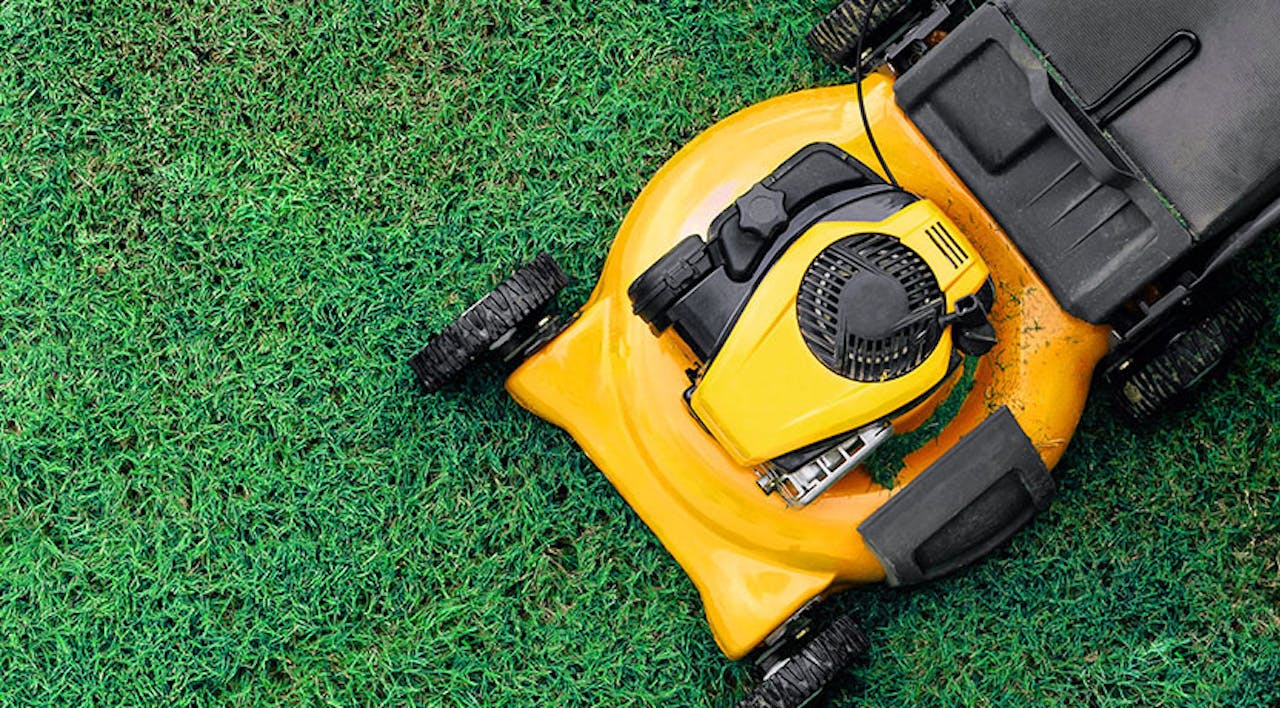