Products > Precision Components
Cold-Formed Micro-Components
Cold-heading uses applied force to punch metal blanks housed within a die, forming the desired component shape. The applied pressure causes the plastic flow of metal until the blank assumes the shape of the space within the die. This is a cost-effective option since heat treatments, shearing and other secondary processes are not necessary for the construction of simple components.
Some examples of cold-formed micro components include Kovar pins, micro eyelets, micro electronic components, micro contacts, cold-headed pins, and other micro or small components.
Learn more about the advantages of cold forming as well as how this process works.
CUSTOM MANUFACTURING
Custom Micro-Components
MW Components specializes in the production of micro and miniature metal components. Cold-heading is often used to make high volumes of mission-critical parts that are stronger and more precise. Our 30 plus combined facilities have the right materials, technology, machinery, and industry experience to develop the perfect component for your application. Our experts work with exacting standards and tight tolerances, and many of our facilities maintain industry-specific certifications that ensure added precision and quality assurance.
To send us your specs or configure a part, request a custom quote.
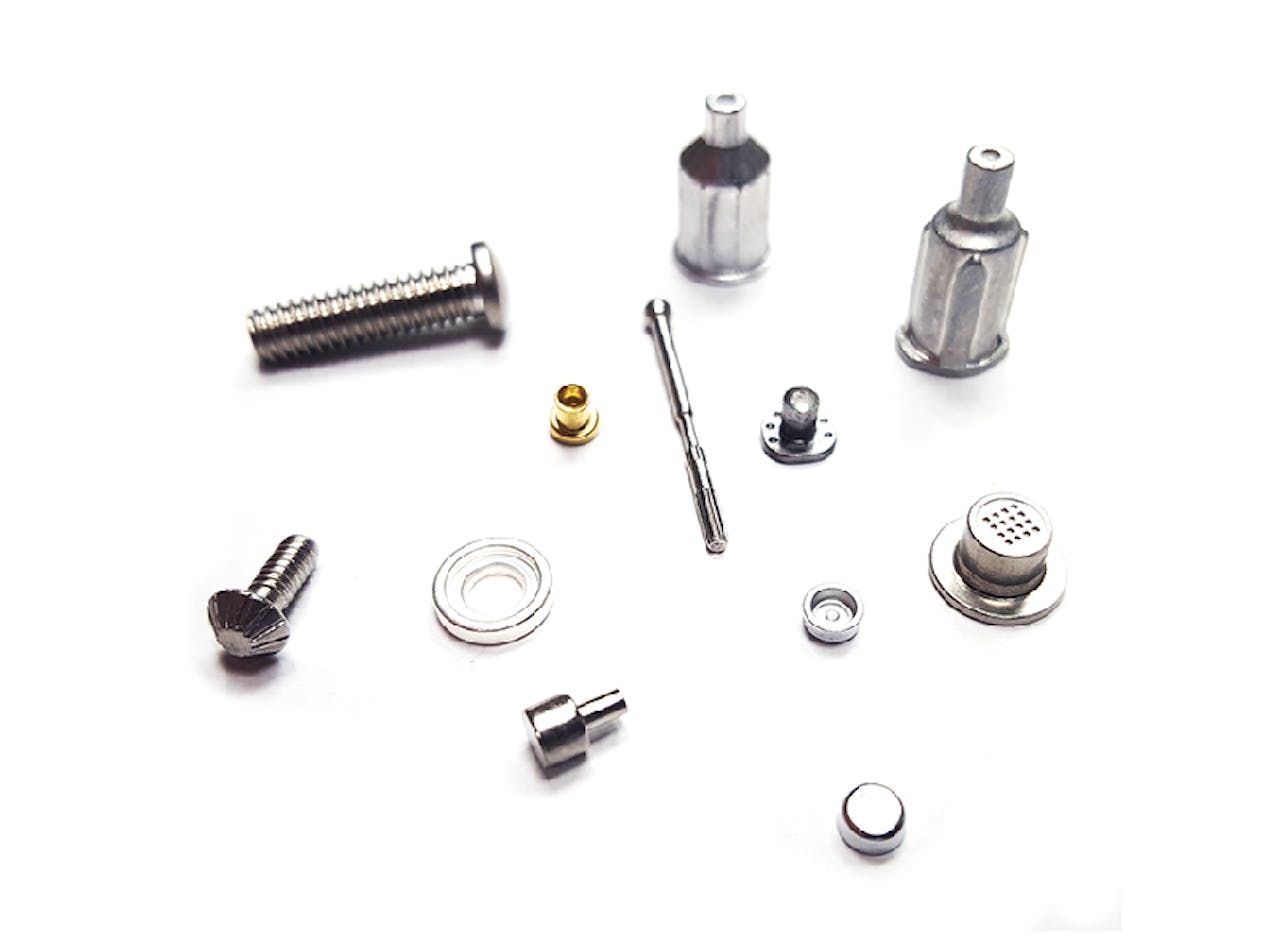
How Does It Work?
Characteristics
New product development teams are always looking for ways to make their electronic devices smaller, appliances more reliable, vehicles safer, or instruments more precise. These products often call for highly engineered metal components on an increasingly miniaturized scale, and the demand for these miniature and micro metal components is accelerating. Those developing such products have a variety of choices in sourcing these components, seeking to meet critical functional specifications to assist with design for manufacturing (DFM), design for assembly (DFA), quality and cost.
That's where MW comes in. We are experts in the field of small component manufacturing, many times using a process that is often overlooked—cold-heading or roll-forming.
Advantages of Cold-Forming / Cold-Heading
There are several advantages to using cold-heading / cold-forming technology over standard machining processes.
- Cost savings through scrap reduction
- High production rates with tight tolerances
- Consistent, reliable quality
- Increased material strength
- Eco-friendly alternative
Resources
Have Questions?
Talk with our experts today and let us help you figure out the best solution.